In recent years, supply chain strategies have come under severe examination, particularly as companies confront worldwide disruptions, adjusting tariffs, and growing transportation costs. Two concepts, notably nearshoring and reshoring, have gained support as realistic approaches to strengthen supply chain resilience and minimize logistical difficulties. As organizations rethink their manufacturing and distribution routes, these techniques are presenting new pathways to decrease costs, enhance response times, and maintain high-quality standards. Let’s take a deeper look at how nearshoring and reshoring might positively affect supply chain management.
What Is Nearshoring?
Nearshoring refers to shifting business activities or manufacturing closer to a company’s major market, frequently to adjacent or surrounding nations. For instance, a U.S. corporation may opt to transfer production to Mexico or Central America rather than sourcing from Asia. By locating manufacturing closer to the customer base, organizations gain from shorter lead times, increased connection with suppliers, and reduced exposure to long-distance transportation interruptions.
One key advantage of nearshoring is the decrease in shipping costs and transit times. Less time spent in transportation equates to faster turnover, enabling enterprises to adjust to market demand more effectively. Additionally, proximity allows businesses to oversee operations with greater ease, which can mean quicker identification and resolution of potential issues in production.
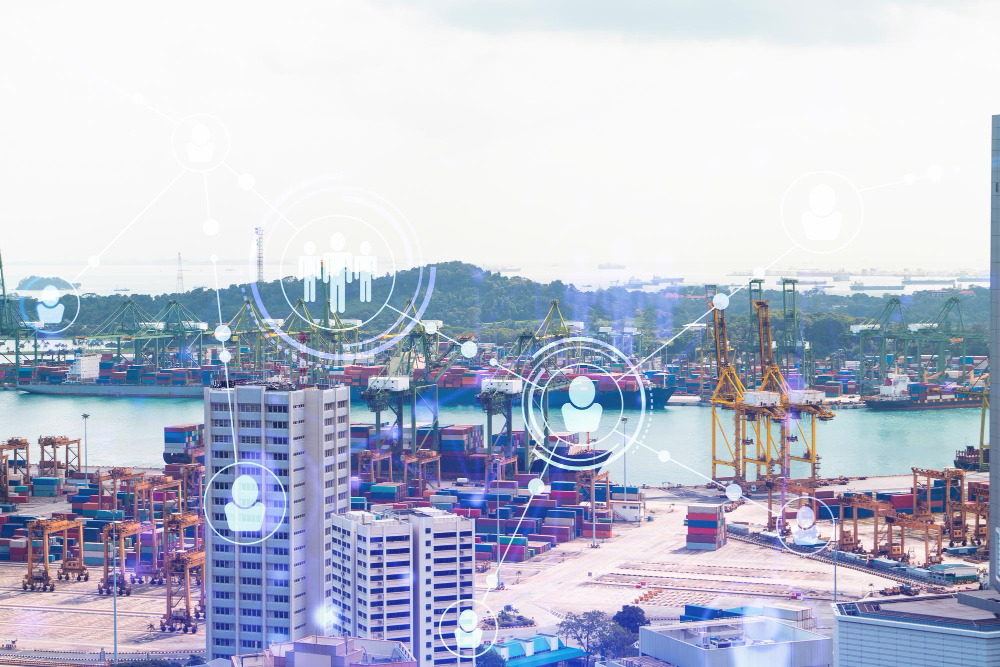
What Is Reshoring?
Reshoring, on the other hand, involves returning manufacturing and production back to a company’s home nation. For many firms, reshoring provides the possibility to reestablish tighter control over quality and production schedules. Labor costs may be greater than in offshore locations, but reshoring gives some benefits when it comes to agility and adaptability.
For U.S. corporations, reshoring manufacturing operations means no longer having to contend with import duties or customs delays. The pandemic exposed weaknesses associated with depending too much on offshore manufacturing, and reshoring may serve as a preventative measure against similar scenarios in the future.

Key Benefits of Nearshoring and Reshoring
Cost Savings on Shipping and Tariffs: Transportation costs have climbed substantially in recent years, making it increasingly expensive to import goods from faraway regions. Nearshoring or reshoring can reduce these costs significantly, often offsetting higher local production expenses.
Improved Quality Control: Proximity to manufacturing facilities allows businesses to conduct more frequent quality checks. When issues arise, quick interventions are possible, preventing costly recalls or product delays.
Faster Response Times: Shorter supply chains mean faster delivery to the end customer, which can enhance customer satisfaction and drive loyalty. Nearshoring and reshoring make it easier to respond to changing consumer demands and market conditions without the delays associated with overseas shipping.
Enhanced Collaboration with Suppliers: Closer geographic proximity to suppliers fosters better communication and collaboration. Nearshoring in particular allows teams to share information, address challenges, and make adjustments more seamlessly.
Reduced Environmental Impact: Shortening supply chains helps reduce the carbon footprint associated with transportation. For companies focused on sustainability, reshoring and nearshoring offer concrete ways to minimize environmental impact.
How to Decide Between Nearshoring and Reshoring
Choosing between nearshoring and reshoring depends on various factors, including cost, proximity to markets, labor availability, and product type. Nearshoring tends to work well for industries that need rapid turnaround and closer collaboration, like automotive manufacturing, electronics, and textiles. Reshoring, meanwhile, can be ideal for high-tech products, custom manufacturing, and industries sensitive to import restrictions or tariffs.
Cost considerations are, of course, at the forefront. While labor costs in a nearshore or reshored location may be higher than in offshore alternatives, the savings in shipping and the value of increased control can tip the balance. For some businesses, moving operations back home is as much about boosting the brand’s image and supporting local economies as it is about pure dollars and cents.
Real-World Examples of Nearshoring Success
Several well-known companies have successfully implemented nearshoring strategies.
Boeing’s nearshoring operations are carried out in a new facility in Chihuahua, which operates as an aircraft wiring plant. And as of last year, the Chihuahua plant produces 95% of all the wiring on Boeing’s 787 Dreamliner.
Back in 1996, Toyota nearshored one of its production units to Thailand. And today, it now operates three plants in the country.
Back in 1987, Whirlpool nearshored much of its operations to Mexico. Whirlpool’s Mexican facility exports 80% of machines to the US and Canada.
Foxconn reportedly moved some iPad production outside of China for the very first time.
These moves are made to capitalize on quicker delivery times and reduced transportation costs. As a result, they have witnessed a marked improvement in their ability to adapt to changing market needs.
The reduced lead times and enhanced quality control added to customer satisfaction and built loyalty.
Your Partner in Supply Chain Optimization
Whether nearshoring or reshoring makes the most sense for your business, Source One is here to help make the transition smooth and strategic. We specialize in supply chain consulting, providing expertise in optimizing your logistics to support efficiency and responsiveness. From supplier selection and risk management to cost analysis, our team at Source One ensures that your supply chain meets the demands of today’s marketplace.
If you’re considering making a shift, let’s work together to analyze your unique situation and determine the best approach. Source One is committed to helping you achieve a supply chain that not only supports growth but also withstands the challenges of the global market.